From 3D Geometry to morse code, an inside look at our product development.
We sat down with Durisol’s Product Development Manager, Mac Readhead to get the inside scoop on his role and what product development looks like at Durisol. From 3D Geometry to morse code translations, Mac tends to be involved in anything that is not considered a “typical” noise wall project.
Product development is broad and varies across industries. Can you describe your role on Durisol’s Product Development Team?
I help the business in several capacities. I work with others to produce product submissions to local transportation regulatory bodies such as Ontario’s Ministry of Transportation (MTO) or US State Department of Transportation (DOT).
During my day-to-day, I am involved with everything weird and wonderful. If a customer wants wall customizations to represent the region in a meaningful way or need a product to better suit their surroundings, I work with the rest of the Durisol team to conceptualize and deliver the vision they came to us with. For example, these requests could be a piece of custom artwork on an Absorptive Noise Barrier panel, a custom panel production system to produce 10+ Ton panels with unique shapes (Currateau*), or like last year when I developed a bird screening pattern that used morse code translations of all Metrolinx GO Stations in the Greater Toronto Area (GTA).
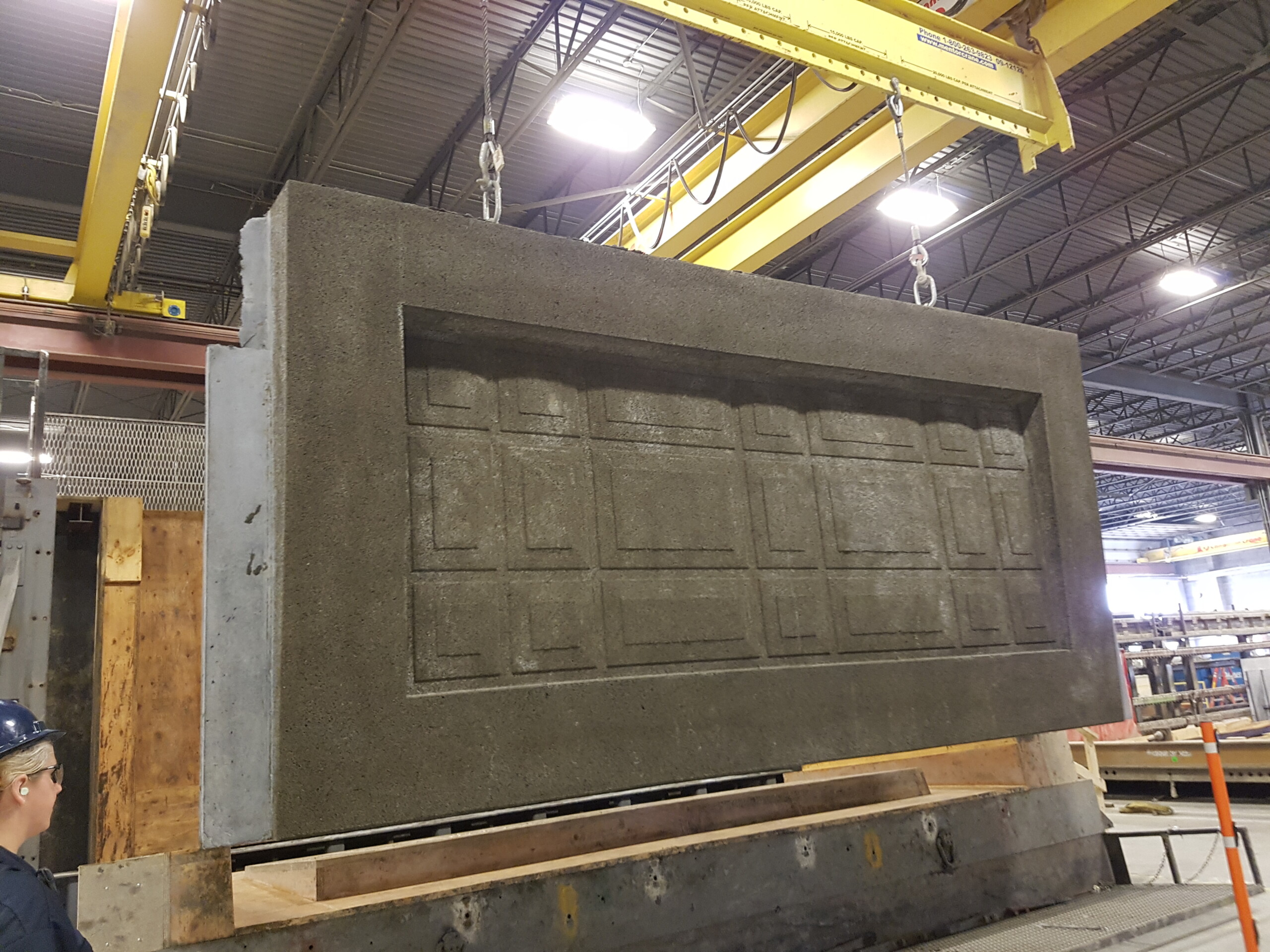
*Pictured here are the unique shapes from a previous project we completed in Curatteau, Montreal.
What stage of a noise wall project are you involved in and how do you work with other team members?
I’m not typically involved in our standard projects. However, when a customer asks for customizations, I’ll work with our Technology Manager, Kurt Lindemann to develop 3D Geometry for a custom mold, or work with our Director of Engineering, Boris Karanfilovski and his team to design a portion of the system.
What goes into introducing a new product?
Every product calls for its own approach. We might have an entirely new product line where new details and standards are developed from many months of revisions and testing, and in other cases it may be a revision to an existing system, like evolving our MASH TL-4 structure mounted system. I try to set up the Sales, Design and Estimating teams for success with as much information about the product as I can so that they can be quickly knowledgeable on the product, as well as be comfortable utilizing it.
“I work on prospective new products from Concepts, Design, Prototyping, Simulation, Renderings and, if we’re lucky, I get to have a car thrown at it.”
What is the project that you are most proud of? Why?
I don’t think I could choose one, because so many aspects of my job have impacted both me and the business in different ways.
Once I learned that I could render 3D models 5 years ago, I used to stay 30-45 minutes late several days a week to practice on the product models we had at the time. Every morning I’d review them with Jordan Divinski, Senior Draftsperson and discuss the aspects that would add more realism to the scene, or object. For another project of ours with Metrolinx, they accepted our patterns simply with the renders I created saving both parties time and money. We’ve also rendered our noise walls onto highway bridges that wowed the client enough to want to work with Durisol. I still render our products now and have learned countless methods to produce them better and better each time.
Developing custom designs always comes with a rewarding feeling. For one Metrolinx project, I had to create several patterns in 3D for our Technology Manager, Kurt to make molds for. The more that I do, the more I learn about what to be cognizant of while creating them, from panel split management, mold relief angles, pooling of sediment/water, lighting shadows…the list goes on.
One of my favorite newer system designs is the revision to the MASH TL-4 Structure Mounted Noise Barrier. As a former draftsperson, I had a lot of hands-on experience with the previous design. I was able to take feedback from site installation partners, procurement, project managers, industry experts and the engineering team to make a more streamlined system that’s not only simpler to design and install but is safer for passing vehicles.
As a more tenured employee, what keeps your job interesting?
As you might have noticed by now, there’s not a day that goes by where it’s the same thing for me. I’m continually challenged to come up with new designs and ideas to either solve a current issue or propel the business forward in new avenues.
What are you working on right now?
Sorry, but that’s classified. You’ll just have to wait and see.